Vacuum Casting: Prototype & Series Production Through Silicone Mold Duplication
Vacuum casting is a manufacturing technique used to duplicate parts from a silicone mold. Starting with a 3D-printed master model, liquid plastic solidifies inside the mold, enabling the creation of prototypes or small series productions.
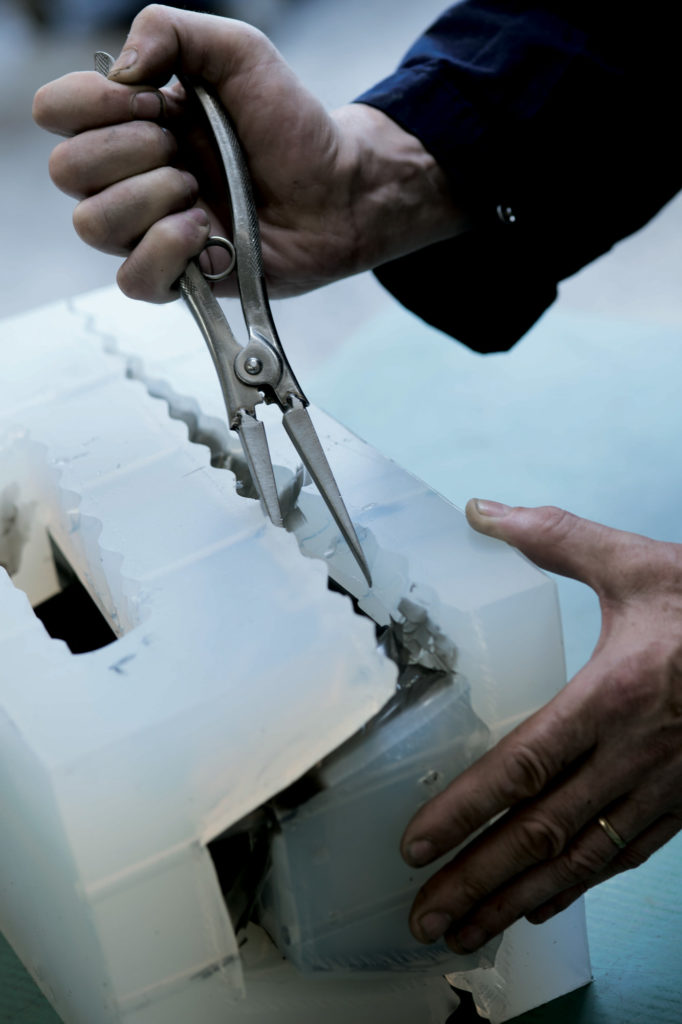
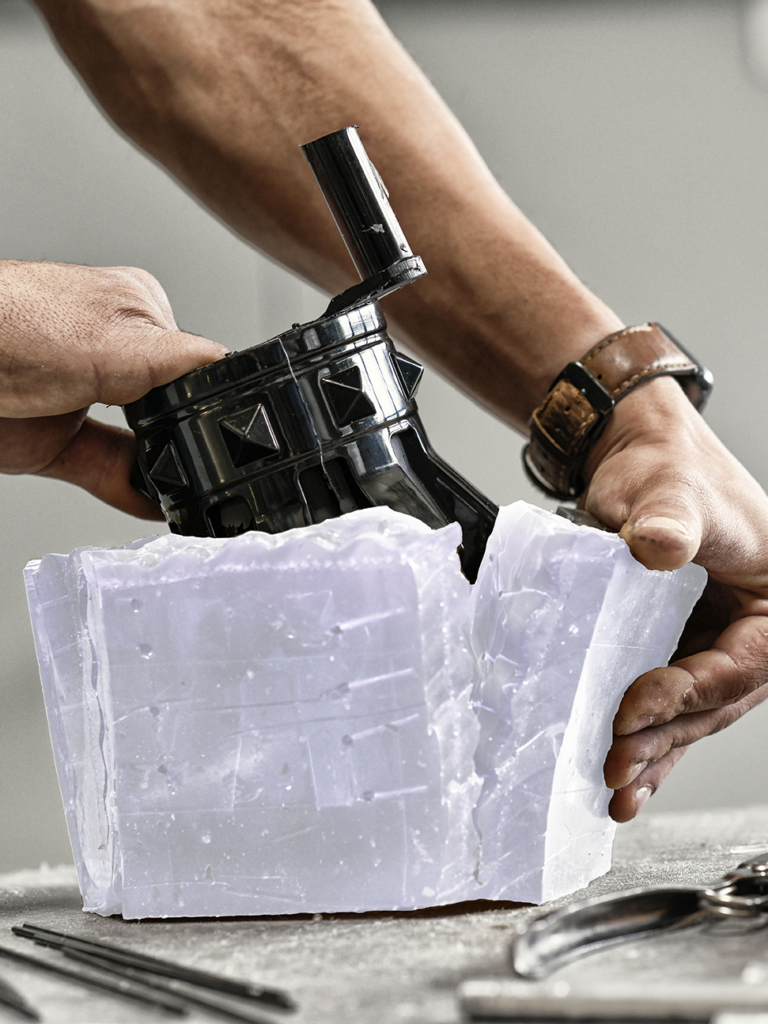
Prototype Duplication & Short-Series Production
Polyurethane parts produced via vacuum casting offer mechanical, thermal, and aesthetic properties comparable to injection-molded plastics. This process provides a wide range of materials, hardness levels, and colors, making it highly versatile.
Ideal for prototypes, assembly testing, marketing samples, or small production runs, this technology is particularly well-suited for short series production due to the limited lifespan of silicone molds.
The MMB VOLUM-e Advantage:
- Unparalleled Material Variety: MMB VOLUM-e offers a vast range of materials, including: Dual-hardness combinations within a single part, tinted glass-like effects for luxury prototypes, transparent finishes, textured surfaces, such as faux leather for the automotive industry
- SLA & Vacuum Casting Synergy: Stereolithography (SLA) enables the rapid production of high-precision, smooth-surfaced master models, perfect for vacuum casting (VC). This ensures flawless replication through counter-molding.
- Medical & Food Compatibility: Our vacuum casting processes utilize polyurethane plastics certified for food and medical contact, ensuring compliance with strict industry regulations.
- Industrial-Scale Capabilities: With a fully integrated vacuum casting production line, including large-format equipment and in-house processes (master model production in SLA, polishing, machining, painting), MMB VOLUM-e ensures fast, high-precision, and high-quality plastic parts.
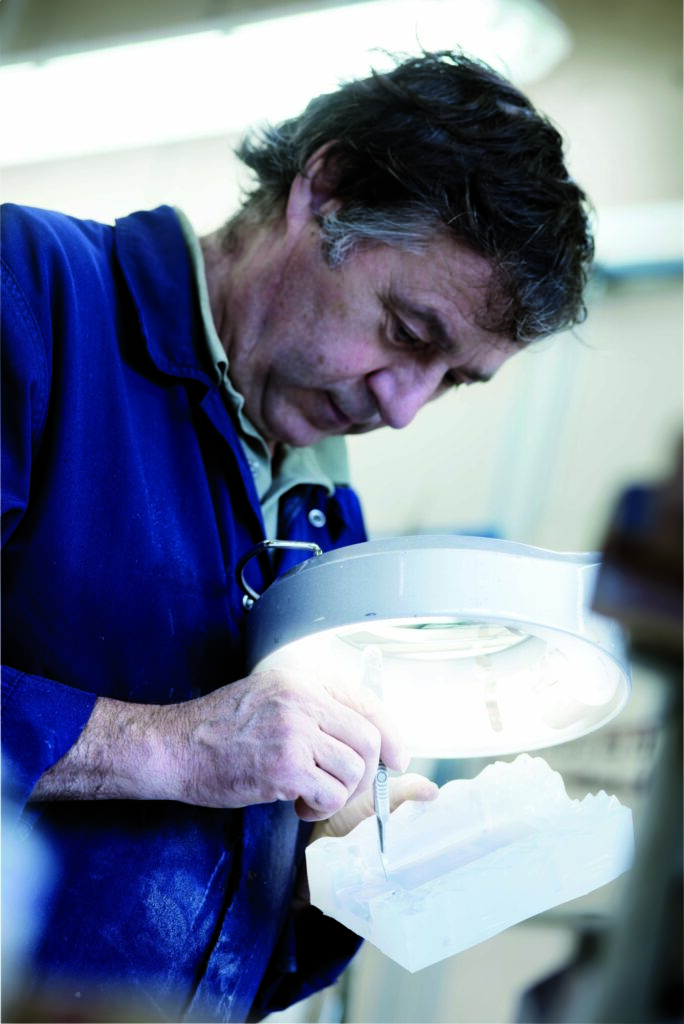
Extensive Material Options & Large-Scale Production
Our vacuum casting team offers a broad selection of materials, from soft to rigid plastics, with a variety of finishes and large-format part capabilities.
Equipment & Production Capacities
- 6 vacuum casting machines, maximum dimensions: 3000 × 1000 × 800 mm or 17L
- Material options: Rigid & flexible polyurethane, transparent & tinted-through plastics, biocompatible & flame-retardant materials, multi-material combinations.
- Finishing capabilities: Sanding, polishing, sandblasting, cabin painting & metallization